
BeSoGreat – Brewer’s spent grain biocomposites for biodegradable plastic products through injection molding and
3D printing
In the cross-border project BeSoGreat we are working together with partners from research institutions and industry to contribute to a sustainable and circular economy and strengthen the alpine region. By implementing a ‘Circular Business Model’ for brewer’s spent grain, a by-product of beer production is turned into a valuable raw material for bioplastics. On this basis, biocomposites are developed and used to manufacture technical products via 3D printing and injection molding, closing the sustainable circle from material development to application.
This project is co-funded by the European Union (Interreg Italia – Austria ITAT-11-012).
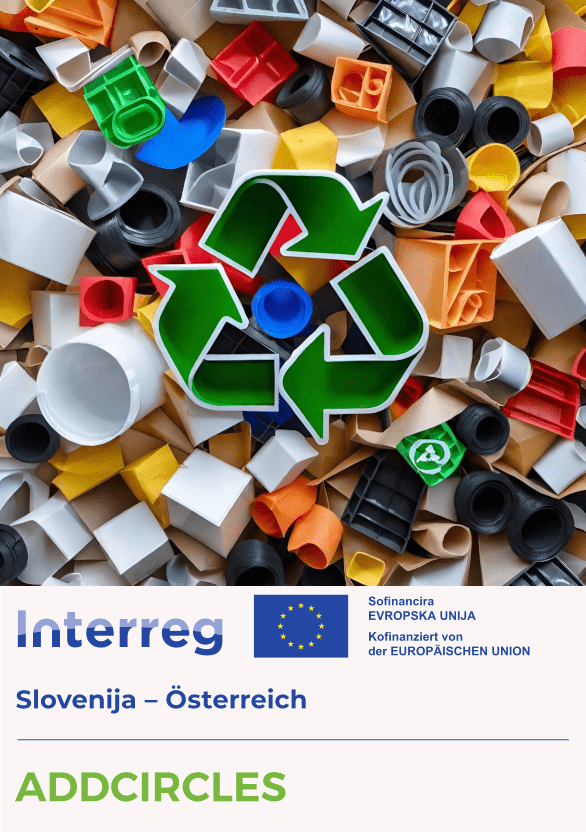
ADDCIRCLES – Promoting Sustainable Regional Development through Additive Manufacturing: A Cross-Border Initiative for a Resilient and Circular Economy
The main objective of ADDCIRCLES is to empower regional companies and networks for additive manufacturing (AM). The technology is perfectly suited to the region’s business landscape, enabling the production of high value-added products through the development of sustainable solutions. As such, ADDCIRCLES will stimulate the region’s transition to a resilient and circular economy. ADDCIRCLES aims to drive the implementation of AM in a way that improves resource efficiency in manufacturing and promotes recycling and the use of natural materials. The objective will be achieved through the establishment of a collaborative network of different transboundary value chains and two pilot projects on knowledge transfer at different stakeholder levels. Read more on the project website.
This project is funded by the European Union (Interreg Slovenia – Austria SIAT00036).
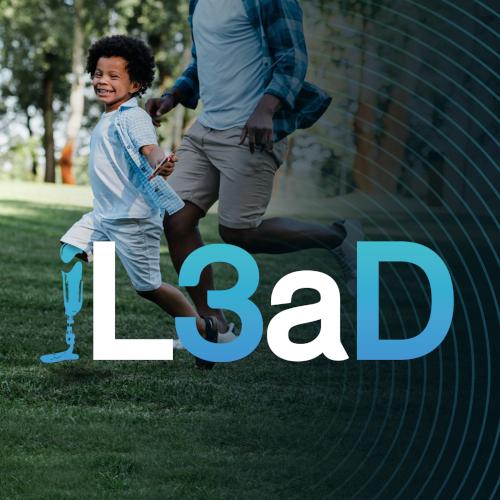
iLEAD – Lightweight Functional and Hybrid 3D-Printing for Medical Assistive Devices
In this project, we aim to fill the gaps in the current 3D-printing technology to fabricate medical assistive devices with significant user benefit, well-being and availability. We develop methods to enable hybrid material and (spatial) full 3D-printing of optimized lightweight lattice structures. Additional functionality is added by embedding sensor and actuator concepts during the design process. The technological developments are accompanied by a continuous user-centered-design process to fabricate devices which meet user needs. Read more on the project website.
This project is funded by FFG (Austrian Research Promotion Agency) under contract no. 884136.
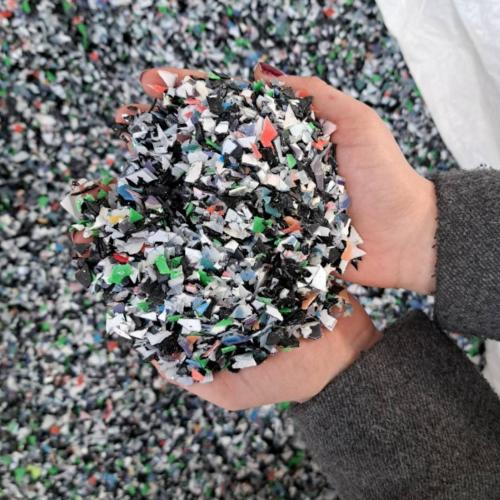
Flake-and-Print – 3D printing of recycled plastic flakes and granules for visual and mechanical complement of furniture elements
Since recycling plastic waste can avoid large amounts of climate-relevant greenhouse gases, Trastic GmbH has set itself the goal of upcycling plastic waste into individual and high-quality furniture. To this end, it has developed a process for manufacturing furniture panels from recycled plastic. However, only relatively simple geometries can be produced with the developed process. Therefore, the goal of this project is additive manufacturing of parts with more complex geometries that visually match the pressed furniture and have mechanical integrity.
This project is funded by FFG (Austrian Research Promotion Agency) under contract no. 901249.
PROTEA – Prostheses and Medical Aids with Enhanced User Acceptance through 3D-Printing and Functionalization
Women are less likely to be equipped with a prosthesis than amputee men. When women are equipped with a prosthesis, prosthesis fitting fails more often and prostheses are less likely to be accepted and used. PROTEA aims to improve the accuracy of fit and acceptance of prostheses and thus contribute to closing the existing gender and diversity gap. Key innovations here are a digital manufacturing process, innovations in materials and structure through 3D printing of the outer socket as well as a soft body with integrated sensor technology. Read more on the project website.
This project is funded by FFG (Austrian Research Promotion Agency) under contract no. 897348.

Nanogoes3D – Nanomaterials and Additive Fabrication of Adaptive Structures for Smart Human Device Interfaces
Nanogoes3D combines different disciplines for the development of 3D-printed soles for individualized shoes in the sports sector. The combination of nanomaterials and 3D printing technology allows in achieving flexible, lightweight, cost-effective smart shoe insole with antibacterial properties. The research is categorized into three areas: a) development of suitable nanomaterials for sensor and antibacterial properties; b) design and development of 3D insoles with excellent physical and mechanical properties; c) development 3D printed smart insole demonstrator by establishing the optimal user-interfacing concept based on FEM simulations.
This project is funded by FFG (Austrian Research Promotion Agency) under contract no. 890606.

AMASE – Additively Manufactured Sensorized Prosthetic Liner Systems
The aim of AMASE is to create a unique and imperceptible measurement system that is compatible with existing prostheses, helps avoiding medical complications, aids the prosthetist in finding the best possible fit, provides the physical rehabilitation professionals with means to optimize the rehabilitation process, improves the gait profile, increases the comfort for the amputee and thus increases the overall acceptance. This will be accomplished by creating an additively manufactured sensorized prosthetic liner systems, which includes arrays of novel flexible pressure and force sensors together with integrated off-the-shelf temperature and humidity sensors and interconnected by flexible and stretchable electrodes.
This project is funded by FFG (Austrian Research Promotion Agency) under contract no. 891132.
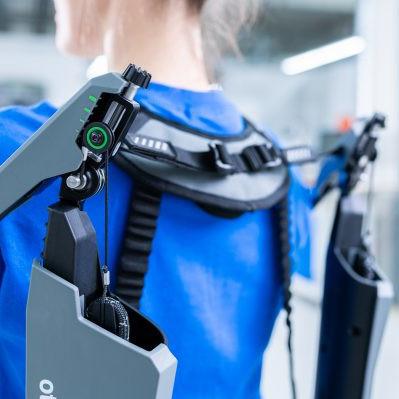
exoATwork – Exoskeletons for Manual Workstations
Manufacturing companies are facing various challenges. The demographic change, the increased working life, the shortage of skilled workers and the product individualization increase the costs. Therefore, the physical support of employees through exoskeletons is becoming increasingly important. The aim of the exoATwork innovation camp is to impart research-oriented knowledge and concrete recommendations for ergonomic and sustainable design of manual workplaces to employees of SMEs and companies in all manufacturing sectors by means of lectures, workshops and practical case studies. Read more on the project’s webpage.
This project is funded by FFG (Austrian Research Promotion Agency) under the FFG-Innovationscamp M program.
Completed Projects
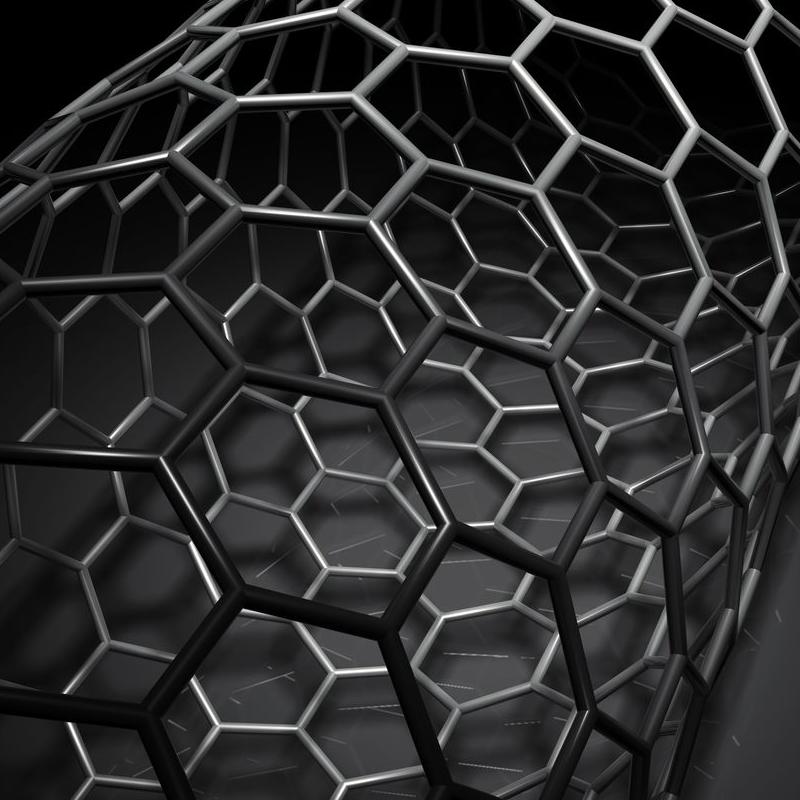
5D-CF – 5-axis printed continuous fibers on a mold
This research aims to explore the potential of 5-axis printing with continuous fibers, specifically by incorporating rotation printing and 3D-printed molds. The goal is to create high-stiffness structures by printing continuous fibers on a rotating mold, which can then be detached from the final product. As there are only a limited number of attempts to integrate these techniques, this research presents a valuable opportunity to advance the field of 3D printing technology.
This project was funded by AWS (Austria Wirtschaftsservice) under contract no. P2409846.
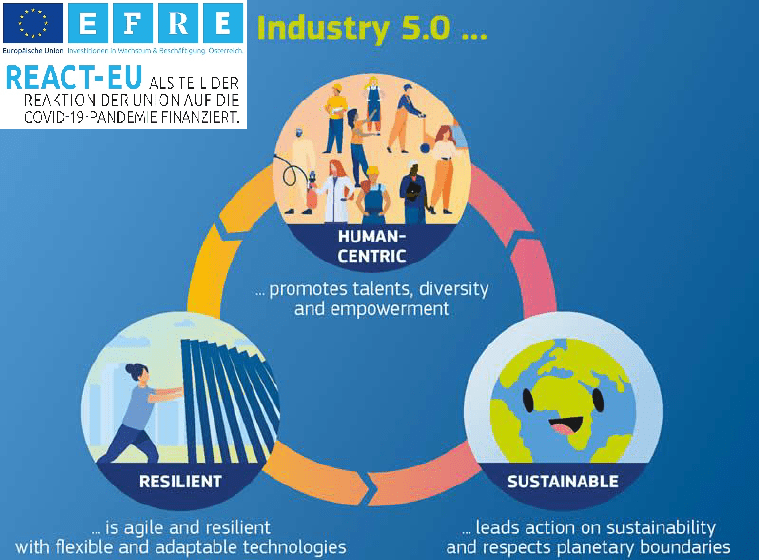
ResilienceTEC
With ResilienceTEC project, CUAS aims at initiating a technological foundation for research projects in the context of Industry 5.0 to promote a more resilient society. Industry 5.0 emerged as a term in response to Industry 4.0, gaining significance amidst the pandemic, sustainability efforts, and a focus on resilience. The approach prioritizes stakeholder value over shareholder value, emphasizing on employee well-being, utilizing technologies for prosperity beyond growth, and respecting the limits of our planet. ResilienceTEC project addresses current megatrends like the climate crisis, carbon-neutral industry, spatial planning, and demographic shifts through the establishment of technological infrastructure in these respective areas. This encompasses technologies for urban planning involving local communities (e.g.,
modeling technologies), the development of decarbonization technologies for
industry (e.g., 3D printing for lightweight construction, technologies for hydrogen energy supply), technologies supporting the health and elderly (e.g., gait analysis measurement systems for stroke patients), and technologies for the development of eco-friendly, smart materials (e.g., testing systems for fiber-reinforced composites).
This project was funded by EFRE and REACT-EU. More information at https://www.efre.gv.at/.
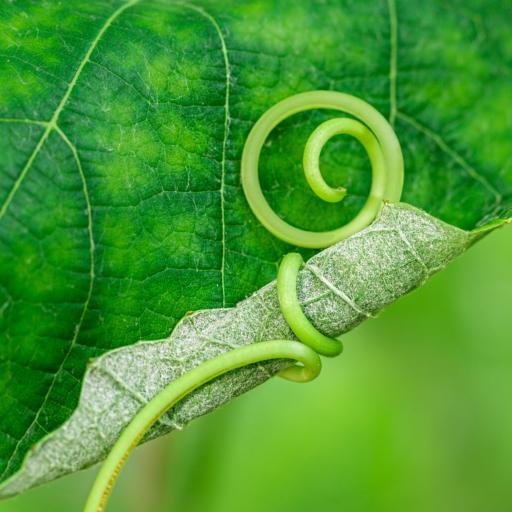
Smarter Leichtbau 4.1 (Smarter Lightweight Construction 4.1)
Lightweight construction in all applications is a necessary aspect to save resources. It enables savings in operation due to lower weight, especially in constructions that are moved in some way. The use of renewable raw materials, especially reinforcing fibres, enables the use of regional raw materials and regional production. The use of sensor technology enables an interface to the digital world and also contributes to further resource savings, as materials can be optimally utilised. The independent EFRE application Smarter Lightweight Construction 4.1 builds on these key points and the results already achieved, and represents a significant new step in the work and cooperation. Read more on the project website.
This project was co-funded by the EFRE European Regional Development Fund.
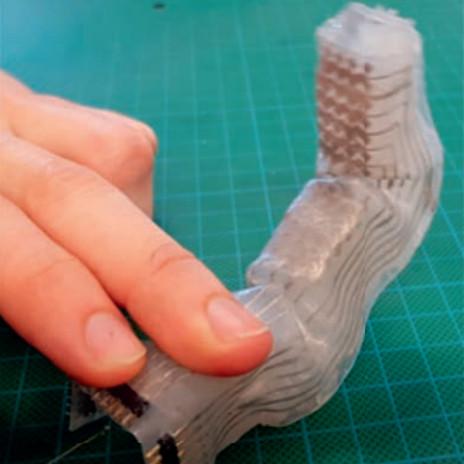
ROSE – Robust Tactile Sensing For Differentiated Robot Haptics
The goal of the research project ROSE is a multimodal, large-area, fully stretchable tactile sensor based on a piezocapacitive principle integrated into soft robotic fingers with mechanical properties optimized based on the material properties. We work on novel gripper and other soft devices design concepts with enhanced sensing and consequently also manipulation capabilities. We further want to pave the way towards an integration strategy of sensors into soft devices in general where we see important future applications in healthcare and medicine such as, e.g., the development of sensorized phantoms. Read more on the project website.
This project was co-funded by the EFRE European Regional Development Fund.
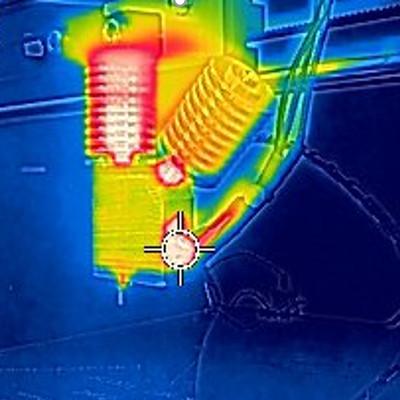
ADPilot – ADMiRE Pilot Line: 3D printing of lightweight components made of fiber composite materials in a robot-based production cell
Continuous fiber composites are ideal for lightweight applications due to their high strength and low specific weight. One of the biggest challenges in industrial use is the labour-intensive manufacturing process, which leads to long production times and high unit costs. One approach to resource optimization is the development of fully automated processes. In the ADMiRE Pilot Line project, 3D printing technology for continuous fiber composites will be set up and integrated into a robot-supported manufacturing concept.
This project was co-funded by the EFRE European Regional Development Fund.
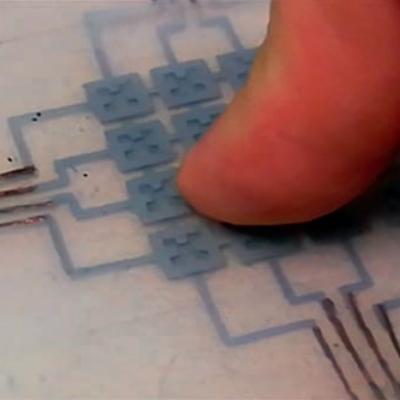
ASAM – Application-specific AM technology: Interreg network for education and rapid prototyping
The two high-tech locations of the Ljubljana Region and the Villach Technology Park both strive for visibility on a supra-regional and European level. Due to the geographical proximity, cooperation between the two regions would be of great advantage in order to increase the number of players (reaching critical mass). There is an opportunity in the area of AM (Additive Manufacturing) technology. The overall project objective is to strengthen cross-border competition, research and innovation by establishing a joint AM technology platform. Read more on the project website.
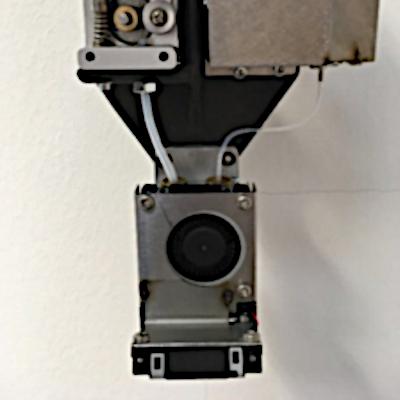
MMO-3D – Innovative 3D printing for high-performance fiber composites
The focus of MMO-3D is the adaptation of a 6-axis robot with an injection moulding technology and a fibre manipulator. This technology enables the production of even geometrically complex products with ultra-high-strength lightweight materials for applications in e-mobility and medical technology. The project thus contributes to the promotion of cross-border cooperation to strengthen research and technological development, competitiveness and innovation. In the long term, all participating project partners from science and industry will benefit from the mutual exchange of knowledge and technology transfer from mechanical engineering and robotics. Read more on the project website.
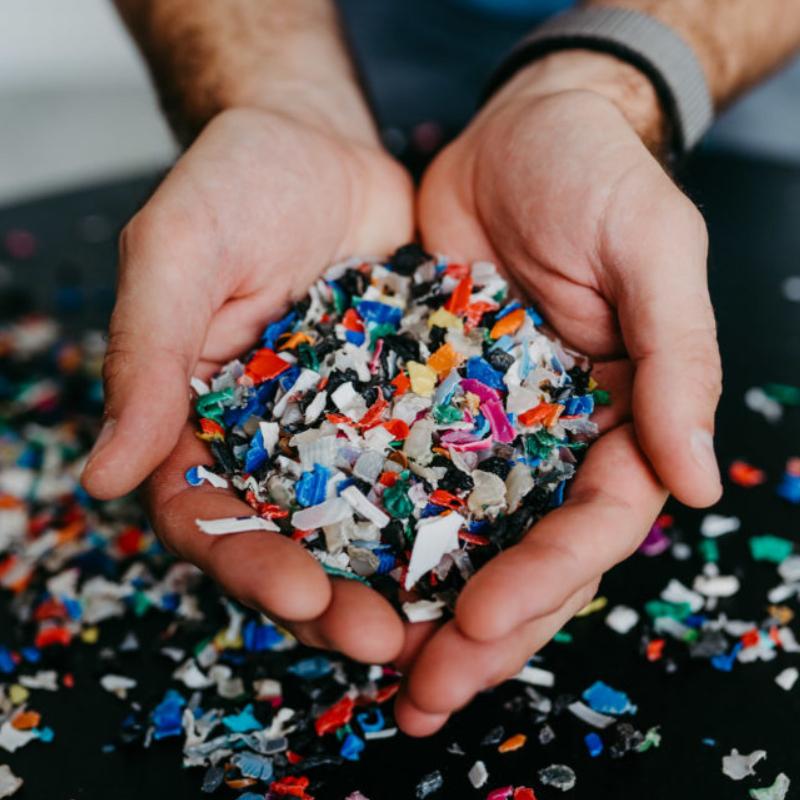
trastic – Innovation Voucher
The Innovation Voucher is a funding instrument of FFG designed to help small and medium-sized enterprises in Austria to start ongoing research and innovation activities. Within the project, the company trastic, which deals with the production of panels (semi-finished products) as a starting material for the furniture industry, was supported in process development. For the production of decorative panels and furniture made of recycled plastic, we researched optimal parameters for the manufacturing process. Link to project partner.
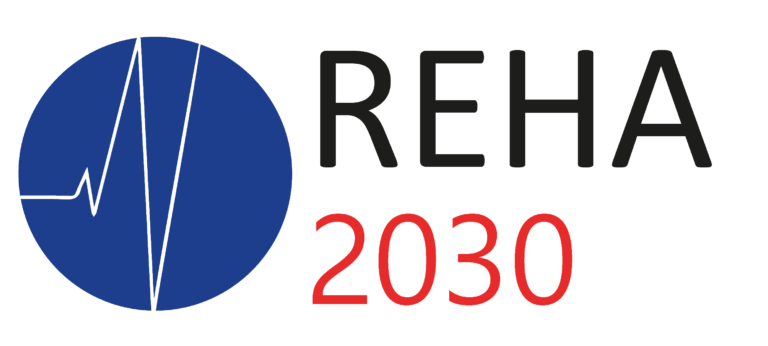
REHA 2030 – A new age of rehabilitation has begun
The focus will be on stroke patients with hand-finger mobility disorders. In iterative development loops, a service model for tele-rehabilitation will be designed with the involvement of various stakeholders: Patients, clinics, therapy centres and therapists, providers of ICT solutions and rehabilitation robotics, insurance companies and other companies in the field of telemedical care. On the other hand, a robotic therapy device for playful, technology-supported therapy is being developed with the involvement of patients and therapists. Read more on the project website.
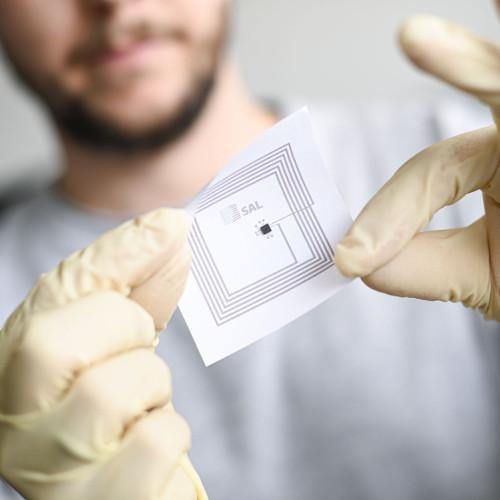
Smarter Leichtbau 4.0 (Smarter Lightweight Construction 4.0)
Due to their property profile, fibre-reinforced plastic composites (FRP) have established themselves as materials for a wide range of lightweight and structural applications. Their high specific strength and specific stiffness combined with low density allow stable components and component structures with low weight. In addition to weight reduction, motives such as energy and resource efficiency, as well as the impact on people and the environment, are playing an ever-increasing role in the selection of suitable materials. Reasons for this are, for example, the reduction of CO2 emissions, the fulfilment of legal requirements or the use of domestic, available raw materials. Natural fibre-reinforced plastics (NFRPs), which have increasingly become the focus of materials research in recent years, offer an ideal combination of high material performance and ecological compatibility. Read more on the project website.